Launch Control and Why You Need It
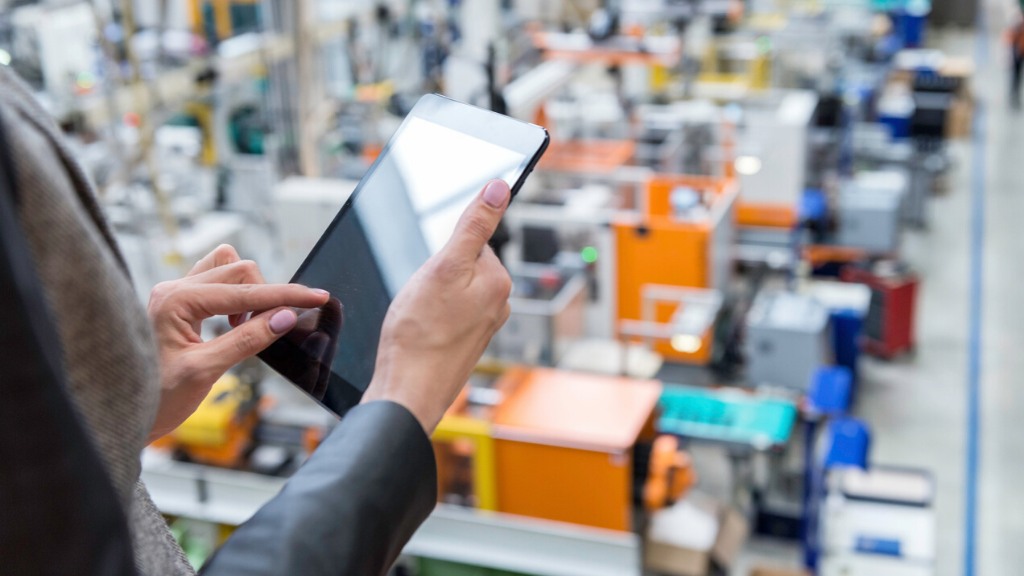
Written By: Leigh Lathrop
In the realities we face today, we need the most detailed picture of supply and demand. That starts with launch control. Not practicing launch control, or launching jobs earlier than required, can present a blurry image of production priorities and the availability of materials and resources to satisfy current demands.
Some companies are good at creating and releasing job orders. In essence, they “launch” job orders in the belief that creating the mechanism for collecting costs and converting materials and resources will create parts. However, this belief is not valid. Simply creating job orders does not ensure we will get parts. Instead, we introduce unneeded demands that the planning engine needs to weed through to present an achievable production plan. That can hinder your production in detrimental ways.
Job orders are a mechanism for collecting data about manufacturing processes that convert raw materials into finished goods using labor and machine resources. They receive the cost of the materials and resources used so that we can then account for the costs associated with the creation of a discreet quantity of items and allow us to relieve inventory for the materials used to produce an item. They also enable us to see the current status of the production process – we monitor Work In Process (WIP) to understand what has taken place and what is yet to happen.
Creating jobs is vital to tracking costs and production. But having too many jobs can create unwanted issues. So, when do you need to have a job order? Right before you are about to perform production transactions.
There are many issues with having job orders before you need them.
Creating jobs that can’t successfully be completed at the time of launch
We need resources and materials available to complete production. With APS, you have the “ready” flag that indicates that all the materials required are in inventory and available to satisfy the demands. Launching jobs earlier than needed will have you spending time trying to determine when the materials are available.
Material shortages can be misleading with job orders
When you have a start and end date on a job order, the system thinks this is when the work will be performed. But if you have shortages, the projected dates do not include the shortage lead times. PLNs give more accurate data on when items that are short may be available.
Maintenance is required on all job orders
Job orders become static data at creation. They have the number of items to be produced, all with descriptions and times for commencement and completion. However, they are created to satisfy demand. If the demand changes, such as quantity, date, or item, or if the demand goes away, we then have a supply mechanism that now needs maintenance. We must go in and maintain the job order to keep up with the changes in demand.
Job orders have priority during planning runs
The logic in the system plans job orders before any other demand in the system. All of the job orders in the system, regardless of start/end dates, are scheduled before any other demand, including those due earlier than some job orders. You could experience a shortage on a near term customer order because the planning logic planned and allocated materials to the job order first. You spend time and energy trying to undo what planning indicates is possible, because you have job orders that are not needed reserving materials far in advance of their need date.
Jobs don’t make parts
Creating a job order will not ensure that production happens. From a practical perspective, open job orders. Filter on jobs with a “Released” status (you may also want to look at “Firm”) and count how many jobs are released. Identify the number of job finishes that are typical for a day.
Then, divide the number of job orders by the finishes. You may want to evaluate your policies on launch control if you have more than two days’ worth of job orders.
An experienced ERP Consulting Firm can help you identify opportunities and assist with the best launch control plan and the ERP systems to support. Decision Resources has been helping manufacturers get the most from their business systems and technology for more than 40 years, and we’re here for you during this time. Leverage our ERP Consulting expertise to help you manage your production effectively and efficiently. Contact us anytime.
Similar Blogs
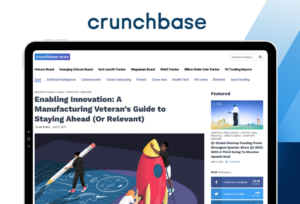
Decision Resources Featured on Crunchbase
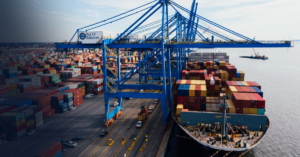
Chips, drugs, and steel — how to prepare for Trump tariffs
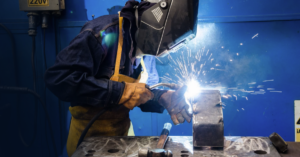