MRP vs. APS and the 5 Reasons You Should Pick APS
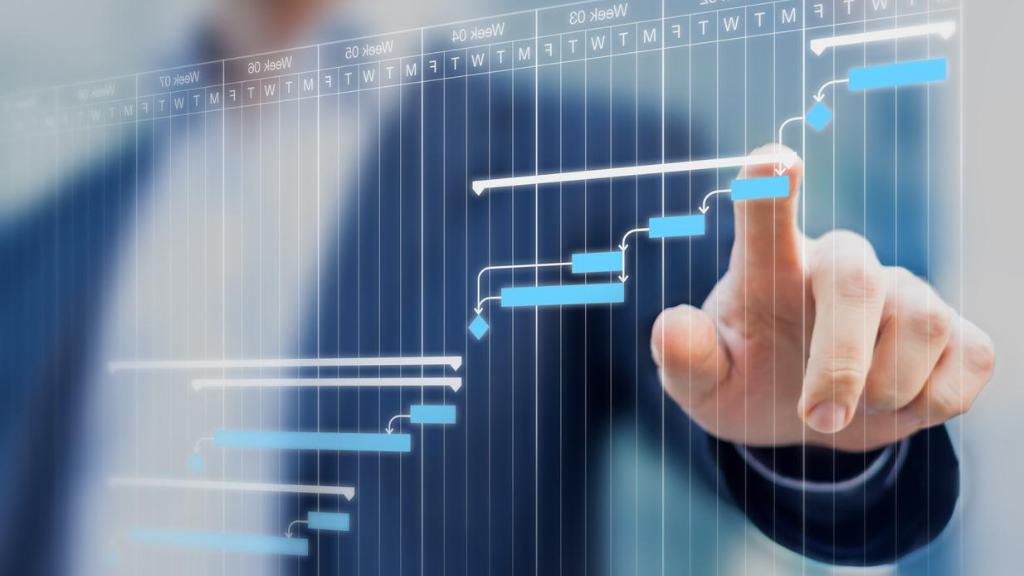
By Leigh Lathrop
History
While Material Requirements Planning (MRP) had its role to play, emerging demands for increased visibility into the planning process, the increase in sophistication across manufacturing and distribution processes, and the improved processing power in Information Systems ushered in the birth of Advanced Planning and Scheduling (APS).
MRP’s fundamental philosophy is back-planning from the demand due date and utilizing an item lead time to provide signals of what to produce or purchase. However, this process gave limited information on whether the schedule of events was realistic and achievable. It also did not “constrain” on shortages of materials, unlike the planning logic of APS.
With APS, this process provides increased visibility to address these issues to meet and exceed promises to customers and their expectations. We want to improve On-Time Delivery (OTD) by creating an achievable Material and Production Plan and then have the tools to monitor and adjust the plan, as needed.
Reason #1 – Planning Order-by-Order
MRP Planning starts at the lowest levels by which an item appears in the Bill of Materials and aggregates the unsatisfied demand to suggest what items need to be bought. Where MRP plans item-by-item from the bottom up, APS plans demand-by-demand.
APS starts with the highest-level demand and plans for material availability and capacity from the due date through the Bill of Manufacturing. It considers not only the material lead times but also the routing times, as shown in the items Current/Job Operations. The logic captures the trail used to identify what supplies will be used to satisfy the demand. Because APS captured the path, we see the linkages between supply and demand at every step along with the routing, and for every item in the Bill of Materials.
This is key. The visibility we are afforded with this map can show us the specific supplies to meet demand. It also shows us the list of what we are “short” to satisfy the demand. More about shortage reporting later.
Another feature of APS is the Order Priority form, which allows us to change the priority by which demands are planned. For example, we can plan Customer Order Demands before planning Forecast Demands. This can be useful to tailor the system to the needs of the environment.
Reason #2 – The Concept of Lateness
While both MRP and APS use backward planning to understand when a material is needed, MRP will not consider the Time Fence of today. If there were tasks that need to be completed in the past (Purchase Order/Job Order launch dates), MRP would tell us that we need to go back in time and perform them on their start date. APS knows we can’t do things in the past.
APS does multiple path planning. Like MRP, it backward plans from the Due Date of the Demand (Customer Order/Forecast/Job Order Due Date), and when it encounters today as the Time Fence, and some demands have not been satisfied, the APS engine begins to forward plan from the date of the longest lead time item for which demand is unsatisfied. We get a Projected Date calculated by the system. The Projected Date is a signal to us: the system is saying that something is keeping us from achieving the Due Date for the demand. How wonderful! The system projects where our issues are before we get to the point of the request being late – hence the title “Projected Date.”
We can see what Demands are projecting late – and we have the tools to drill through the order and see the allocations to identify what is causing the delay. A key set of forms gives us a list of all the demands projecting late so we can identify where we should do work today (focus on the late demands).
Reason #3 – Pegging Visibility
It is all about seeing the connections. When we have an issue (a component will be late, or a job is going to be stopped), we need to be able to drill to the pegging to see the ties between Demand and Supply. We need to be able to see the linkages (the soft allocations) that the planning engine is using so we can:
- See the impact caused by the planned shortage
- See the effects of existing demands if we have an urgent need for a part/component (unplanned demand).
- Determine if we can pull up a Demand. We need to see the supplies (Inventory and Supply Orders) to assess if a pull-up is possible.
In MRP, pegging is a challenge. In APS, the pegging is visible to us and is an essential tool to troubleshoot lateness and improve On-Time Deliveries. We can “see” what is going on with each order.
Reason #4 – Built-In Shortage Report/Capacity Information
APS logic creates a Demand-by-Demand-plan. When it encounters a supply that is not yet in inventory, the system captures that signal and retains a list of shortages – a record by the individual demand. We can see shortages for each:
- Customer Order
- Forecast
- Job Order
These shortage signals can be captured and use to identify:
- Whether we can launch a Job Order (one school of thought is that you never release a Job Order that is short components).
- What elements do we need to chase to satisfy the requirements of the demand?
- What specific items need to be addressed to fulfill the request. It brings a focus on what we need to chase to ensure OTD.
When APS runs Demand-by-Demand, it keeps track of the resources needed to satisfy the demand and the materials. So, we can see the load on our resources without having to engage with a Scheduling engine (another planning toolset). We get Rough Cut Capacity Planning by merely opening a set of forms to show us how APS loaded our resources compared to the Available OnShift Hours for the resources.
Reason #5 – Get ATP
The most important thing we do as an organization is provide the customer a promise date. We commit to deliver products in the right quantity at the right time – our promise. In an MRP environment, we do not have a toolset available to us to determine if our commitment is reasonable. We are taking our history and tribal knowledge to guesstimate what seems to be a reasonable delivery date.
APS creates a virtual database that captures supply and demand information and allows us to perform a “real-time” query of this data to make better promises.
When entering a Customer Order Line into the system, the Customer Service personnel can select the “Get ATP” button and perform a query to look at the new demand. Doing so shows whether we have the materials (and resources for Finite APS) to meet the Item/Due Date/Quantity combination. The system runs a mini planning session and comes back with an answer on whether we can meet the date. If not, we can drill through the demand and identify the constraints/roadblocks that prevent us from achieving the requested date.
With this tool, at the time the order is being entered, we have a chance to see if we will be successful at meeting the promise or where we need to go to work to help get the customer what they want when they want it.
Summary
Demand Planning is all about helping the organization to keep promises and improve On-Time Delivery.
We believe that APS is the toolset that allows us to:
- Make good promises
- Troubleshoot Demands that get into trouble
- Focus our efforts on working on the critical issues that need input – we can see the causes of problems and work to remove constraints and meet deadlines.
When it’s time to upgrade your company to APS, contact the experts at Decision Resources. Decision Resources has been helping manufacturers get the most from their business systems and technology for more than 40 years. Leverage our ERP Consulting expertise to help you manage your production effectively and efficiently. Contact us anytime.
Similar Blogs
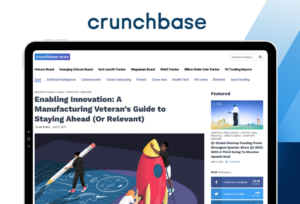
Decision Resources Featured on Crunchbase
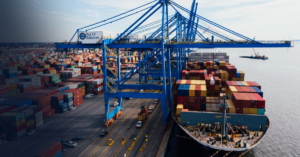
Chips, drugs, and steel — how to prepare for Trump tariffs
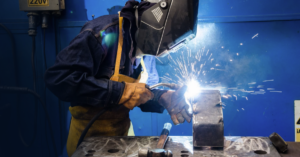